Thank you for an incredible Symposium!
Wow, we’re fresh off a wonderful few days with all of our friends from the Simon Institute and feeling overwhelmed (in a good way) from all the great information, news and resources shared!
The theme of this year’s Symposium focused on “treating janitors as first-class citizens.” We talked a whole lot about strategies to make custodial work safer, more evenly distributed and how we can continue to improve the training we provide. This includes training younger workers in a way that keeps them engaged—not as difficult as you’d think!
A few of the highlights included a special introduction from Annmarie Wilson-Futrell, Director of Building Service for Valparaiso University. She shared some of her journey to learning about the (OS1) System and her excitement for what it will bring her team. Welcome!
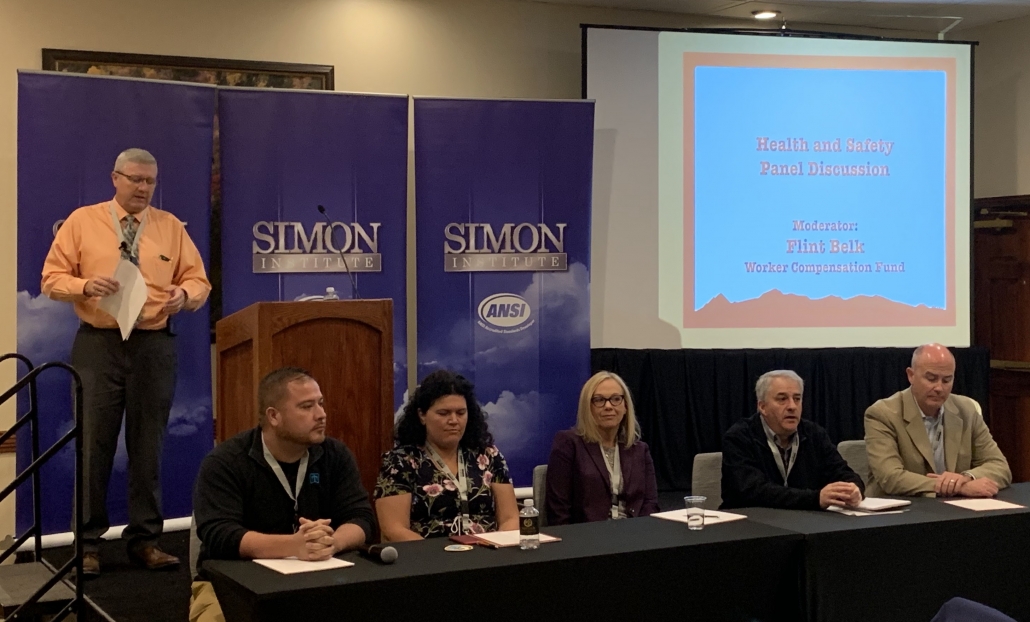
A special thanks to all the presenters, including Dan Weltin, Editor-in-Chief at Trade Press Media Group, who shared new data available in their Cleaning Costs and Frequencies Report which was given to all attendees.
Thank you to everyone who also participated in our first Health & Safety Panel, which provided some interesting insight on safety strategies our users and supporters have in place to help improve safety for custodial teams and workers.
The data and knowledge shared is what makes Symposium so unique to any other industry event. Symposium attendees and presenters are truly the leaders in the custodial services industry!
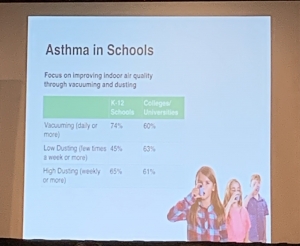
On that note, several very important guests received awards during the (OS1) Awards Banquet and Ceremony. This included five high school students who work as janitors in the evening at the nearby Provo City School District. These students received Outstanding Cleaning Worker Awards, along with individuals from Los Angeles Habilitation House (LAHH), Sandia National Labs and the University of Michigan.
Thank you to our emcee for this year’s events, Alan Wagemester, VP of Operations at GMI Integrated Facility Solutions. In addition to introducing all of the presenters, Alan provided a touching tribute to ManageMen’s late founder, John Walker, ahead of a beautiful slideshow presentation.
Click here to see the Gallery of all the 2019 Symposium Award Winners.
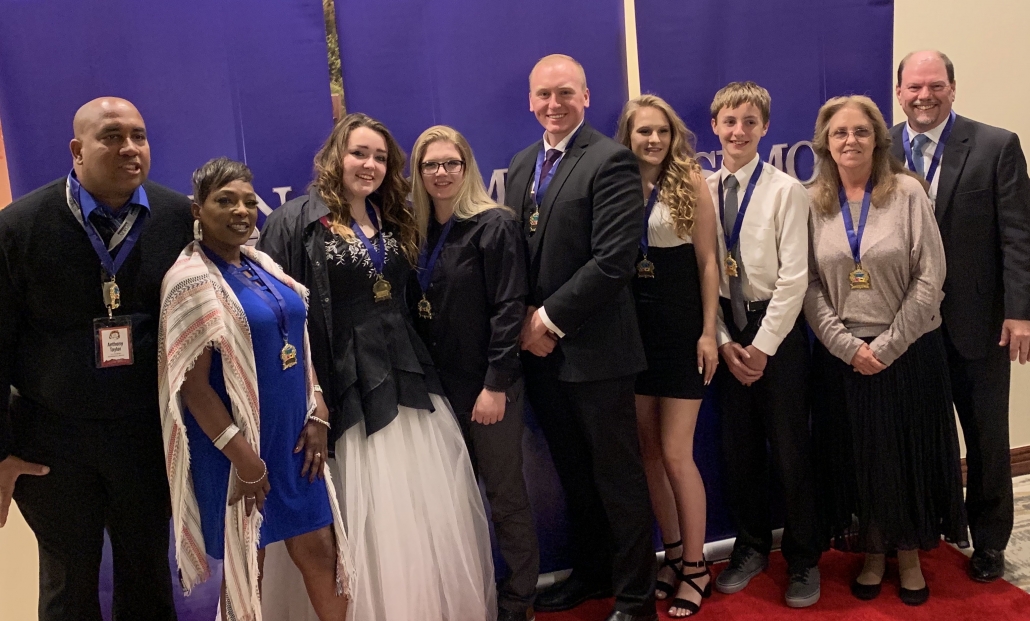
Outstanding Cleaning Workers
Anthony Taylor, Los Angeles Habilitation House
Ryan Beal, Provo City Schools
Jonathan Boswell, Provo City Schools
Shelbi Campbell, Provo City Schools
Natalie Robinson, Provo City Schools
Oaklie Wilson, Provo City Schools
Sara Carillo, Sandia National Labs
Maryanne Cook, University of Michigan
Randi McQueen, University of Michigan
David Oldenberg, University of Michigan
Award Winners 2019
Sandia National Laboratories – 15 Consecutive Years of Audits Above 90% – Milestone
Valparaiso University – Rookie of the Year
The University of Texas at Austin – Sarah M and Charles E Seay Building – Best Audit
Sandia National Laboratories – Safety
Provo City School District – Best Training Program
Sandia National Laboratories – Best Cleaning Team
The University of Texas at Austin – Workloading
Joshua Sego, Michigan State University – Trainer of the Year
The University of Texas at Austin – Best Cleaning Program
(OS1) Green Certified Program of Merit
Los Angeles Habilitation House – U.S. Coast Guard LA/LB
The University of Texas at Austin – E. William Doty Fine Arts Building
(OS1) Green Certified Program of Excellence
Provo City School District – Amelia Earhart Elementary
Sandia National Laboratories
The University of Texas at Austin – Sarah M. and Charles E. Seay Building
We’ll be announcing the dates and location for next year’s Symposium soon! You won’t want to miss it!